PepsiCo en Eneco steken nek uit met hoge temperatuur warmtebatterij
07.03.2023 Simone Tresoor
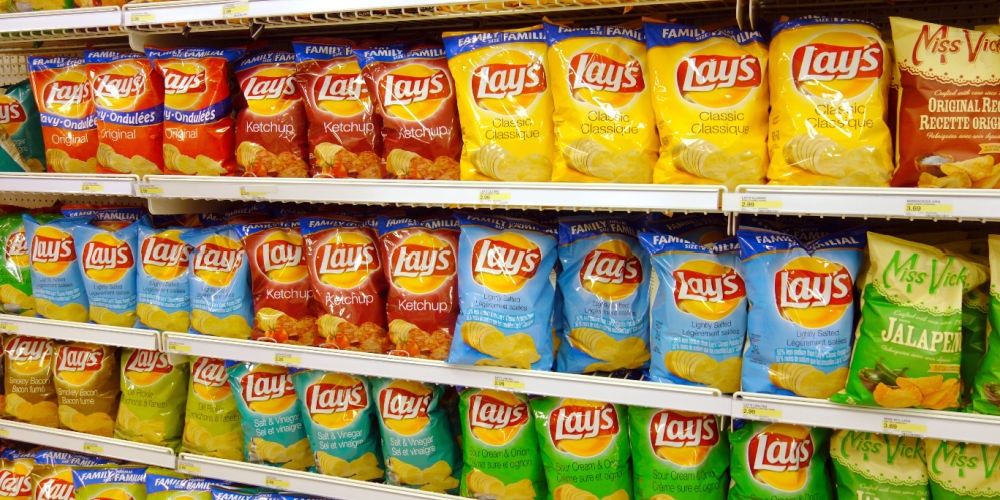
Omschakelen naar duurzame elektriciteit heeft voor de industrie nog veel haken en ogen. Hoe schakel je om naar duurzaam zonder je bedrijfsproces te frustreren? Dat kost tijd, geld en vraagt durf. Wouter de Lille van Eneco en Geert Jan Euverman van PepsiCo vertelden over hun gezamenlijk project: een innovatieve hoge temperatuur warmtebatterij voor de chipsfabriek in Broek op Langedijk, tijdens het EZK-evenement Partners in energie-uitdagingen.
Euverman: “Om van het gas af te gaan bij industrie die intensieve hoogwaardige warmte behoeft bestond eigenlijk nog geen oplossing. Wij denken nu de eerste betaalbare oplossing te hebben bedacht om kostenneutraal van het gas af te gaan en over te schakelen naar duurzame elektriciteit.”
Kraft Block
Om de elektriciteitsprijs zoveel mogelijk te drukken gaat de voedselfabrikant gebruik maken van de dagprijs van elektriciteit. Als de elektriciteit redelijk goedkoop is halen ze het binnen en slaan ze het op in warmte om het te gebruiken voor het maken van chips als de elektriciteitsprijs hoog is.
Hij vervolgt: “Wij hopen op deze manier goedkoper uit te komen dan door met aardgas te verwarmen én onze investering terug te verdienen. Er is een samenwerking gezocht met een Duitse start-up: Kraft Block. In mei dit jaar wordt de eerste paal geslagen en we hopen dat het systeem eind dit jaar kan draaien.”
Hoe werkt het?
Het power to heat-systeem zet elektriciteit om naar warme lucht. De gloeidraad wordt 800 graden Celsius en met een ventilator wordt de warmte verplaatst en opgeslagen in ijzerslak. Als er warmtevraag is draait het proces om. De steentjes dragen hun warmte over aan een lucht-olie-warmtewisselaar. En zo kunnen de chips op 275 graden Celsius gebakken worden. Er hoeft niets te veranderen aan het productieproces. Bij elektrificatie denk je misschien al snel aan een warmtepomp of elektroboiler, maar die halen de temperaturen die nodig zijn in dit productieproces niet.
De Lille: “De samenwerking tussen Eneco en PepsiCo is best innovatief te noemen. We zijn al twee jaar bezig om te kijken of het haalbaar is. We hebben een gezamenlijke business case gemaakt waarin we hebben afgesproken elkaar te helpen. Het is nog niet eerder gedaan en daardoor vrij risicovol. Je verdient de investering niet zomaar terug.”
De fabriek mag er zo weinig mogelijk van merken
“Wij vinden dat wij, als een van de grootste levensmiddelenketens van de wereld, hiermee aan de bak moeten. PepsiCo wil in 2040, dus tien jaar eerder dan verplicht, klimaatneutraal zijn. Eneco heeft gekeken hoe ons afnameprofiel past in het productieprofiel en omgekeerd. Voorwaarde was dat de chipsfabriek er zelf er zo weinig mogelijk van gaat merken”, vertelt Euverman.
Wel moet netbeheerder Liander de elektrische aansluiting van de fabriek verzwaren. De batterij zelf komt buiten de fabriek te staan en kan in twee weekenden worden aangesloten op het warmtesysteem van de fabriek in Broek op Langedijk. Daarna gaat Eneco de batterij strategisch in zetten om zoveel mogelijk duurzame warmte op te wekken tegen zo laag mogelijke kosten.
Risicovol
Voordat er voor deze techniek gekozen werd zijn er vijftien andere technieken bekeken. Er werd beoordeeld op techniek, footprint en kosten. Kraftblock is het geworden met name door de extreem hoge temperatuur die bereikt kan worden.
De Lille: “PepsiCo is wereldwijd het eerste bedrijf dat dergelijke oplossing gaat ontwikkelen en uitproberen. Dat is risicovol. Je hebt durfkapitaal nodig. Het is technisch mogelijk, maar het moet ook financieel haalbaar en in tien tot vijftien jaar terug te verdienen zijn.”
Vier uur warmte
Het eerste plan is om met twee units 50 procent gas te besparen. Als dat werkt wil het bedrijf er nog drie units bijzetten om zo 98 procent besparen. De laatste twee procent zit hem in gebouwverwarming, die niet is aangesloten op deze techniek. PepsiCo wekt ook zelf elektriciteit op met zonnepanelen, maar dat is verreweg niet genoeg. Dat wekt slechts 5 procent van de elektriciteitsbehoefte op.
De Lille: “Hoe we de batterijen zo economisch mogelijk kunnen inzetten, is onderdeel van de pilot. We kunnen nu vier uur lang warmte leveren en bij uitbreiding zelfs tien uur. Dat geeft ons de mogelijkheid om zoveel mogelijk duurzaam opgewekte energie ook duurzaam in te zetten en de netbeheerder te ontlasten.”
Bij succes goed op te schalen
Het innovatieve project ontving een Demonstratie Energie- en Klimaatinnovatie (DEI) subsidie. En de Stimulering Duurzame Energieproductie (SDE++) is ook aangevraagd. De Lille: “Als dit project succesvol is, is het heel snel op te schalen omdat heel veel industrie bij dezelfde oplossing geholpen zou kunnen zijn.”
Euverman: “De SDE-subsidie is nodig omdat de stroomprijs momenteel drie keer zo hoog is als de gasprijs. De SDE-subsidie overbrugt die prijsverschillen zodat we alle ruimte krijgen om te experimenteren. Als dit werkt zou het een oplossing kunnen zijn voor al onze fabrieken wereldwijd. De fabriek in Broek op Langedijk is als pilot genomen omdat we hier tegen de stikstofrechten aanliepen en niet meer konden uitbreiden. Door een deel van de productie te elektrificeren worden CO2- en stikstofemissies verlaagd.”